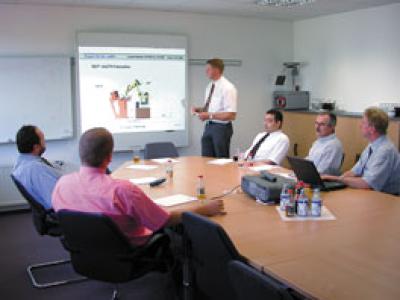
"Genius: 1% inspiration and 99% perspiration." Thomas Alva Edison
Servotak does not believe in the stranglehold of standard gearboxes over design concerns.
When designing a new machine, the market offers endless standarized gearboxes. Brand makes little difference, and pricing, deadlines and performance are the determining factors. Machine design is a slave of the gearbox. This is the conventional wisdom, and leads to conventional results.
However, should you want to make a market defining machine, a custom gearbox is the only solution. The gearbox should accomodate the machine, and not vice versa.
Customer Benefits.
SERVOTAK engineering solutions focus on customers who need custom precision gear units with a superior performance not found in standard market gear units. They provide important customer benefits:
Custom Fit
It is compact, fits exactly the customer requirements and offers better performance than the alternatives.
Time Savings
Our experience in the gear engineering field reduces the total time our customers need to devote to product development.
Development costs under control.
You made the machine, we calculate and design a gear unit within the agreed budget that fits your needs.
Cutting-edge machines.
Our wish is to share your goals and together manufacture more efficient and modern machinery. Our designs can achieve higher precision resulting in reduced cycle time and increased productivity. To sum up, we help you become a market leader.
Who are our engineering services target customers?
- OEMs,
- Machinary Manufacturers,
- Engineering Companies,
- Technology Centers,
- Research and Development Institutes, and
- Universities.
Their common denominator? They all strive to create new, market leading machines. When they need an innovative, cutting edge gearbox, Servotak delivers.
Extensive experience
We are experts in power transmissions of exceptional reliability, innovative design and unmatched robustness .
Our designs appear in a wide swath of the industry: automobile, aerospace, defence, drive systems, food processing, linear systems, machine tools, packaging machines, medical and pharmaceutical industries, robots,...
We are independent
Despite its vast experience, Servotak has always striven to remain independent. We have no vested interests or loyalties. We do so in order to provide vendor neutral solutions.
At a glance, we offer:
Knowledge Consulting |
|
Research |
|
Development |
|
Review & Optimization |
|
Prototyping and manufacturing |
|
Design Philosophy
Reliability |
|
Whole system view |
|
Failure prediction. |
|
Innovation |
|
Full partnering |
|
Competitive advantage |
|
Design process.
The design process is divided into three stages:
Computer analysis:
We calculate gearbox life and durability based on the loads and deflections of gears. We also accurately predict bending and contact stresses, mesh misalignments and meshing forces. We display contact load distribution across the tooth face, contact temperature and micro-geometry analysis.
Thanks to out vast experience in planetary gear units, we understand the importance of equal load distribution between planetary gears, ensuring high reliability and low vibration. By taking into account the effects of assembly, manufacturing tolerances and structure deflections, we predict load distribution through each planetary gear.
Several kinds of analysis are used which deal with, but not limited to, the following areas:
Gear unit |
|
Gears |
|
Shafts |
|
Bearings |
|
Housing |
|
Simulation:
We base our designs and numerical calculation on 3D CAD drawings of the system. We perform FEM (Finite Element Method) analysis for complex gearbox components to guarantee safer and more robust gearboxes. With the results, we obtain:
- Fatigue study.
- Thermal analysis.
- Acoustic analysis.
- Vibration analysis.
- Gearbox life.
Testing:
Prototypes are manufactured at this stage and submitted to various tests:
- Stress test.
- Vibration test.
- Torsional stiffness test.
- Angular gearing
- Friction and wear and tear test.
- Acoustic analysis.
- Lubricant life test.
- Sealing test.
- Extreme conditions test.
- Comparative analysis between obtained and calculated values.